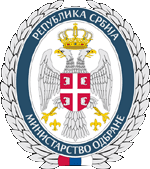
REPUBLIC OF SERBIA
MINISTRY OF DEFENCE
www.mod.gov.rs
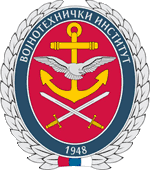
MINISTRY OF DEFENCE
Material Resources Sector
Defensive Technologies Department
Military Technical Institute
www.vti.mod.gov.rs
|
EVALUATION OF STING
DESIGN WITH INCREASED STIFFNESS FOR THE T-38 WIND
TUNNEL
DUŠAN
ĆURČIĆ
Military Technical
Institute, Belgrade, Serbia,
dusan.curcic@vti.vs.rs
MARIJA SAMARDŽIĆ
Military Technical
Institute, Belgrade, Serbia,
majasam@ptt.rs
ZORAN ANASTASIJEVIĆ
Military Technical Institute,
Belgrade, Serbia, anastaz@eunet.rs
ZORAN RAJIĆ
Military Technical Institute,
Belgrade, Serbia,
vti@vti.vs.rs
HABIB BELAIDOUNI
Military Technical Institute,
Belgrade, Serbia,
vti@vti.vs.rs
Abstract:
The T-38 test facility is a blowdown-type pressurized wind tunnel. Large
transient loads during starting and stoping wind tunnel running on high Mach
numbers is common characteristic of blowdown wind tunnels. Stings and all
experimental equipments for the measurements in such wind tunnels have to be
designed for large transient loads. During the supersonic tests a sting is
exposed to large aerodynamic loads and levels of sting stresses and
deflections are high. Sting deflection during the T-38 wind tunnel
experiments has big influence on the quality of measurements. High stiffness
of sting is necessary for model testing. It is necessary to reduce magnitude
of sting deflections to achieve higher accuracy. In this paper is considered
proper material for combination with maraging stainless steel for sting
manufacturing. Carbide metal was selected as material for increasing sting
stiffness. Stainless steel sting with carbide metal core was designed and
manufactured. Finite element simulation of load was performed using software
package NASTRAN NX. Experimental verification was performed by laboratory
measurements of the sting deflections and slopes. Final verification was
performed by the wind tunnel measurements with selected model and stainless
steel sting with carbide metal tube.
Keywords:
deflection, stress, sting, wind tunnel.
|